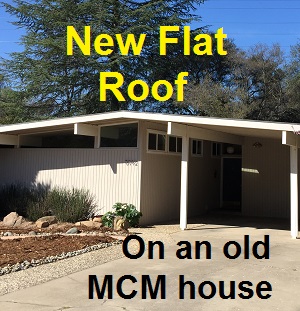
The exterior site lines of a mid-century modern house is one of the hallmarks of this architectural design. The gently sloping, nearly flat, roof that seems to be supported by glass is a key design element for those of us who appreciate this style of modern architecture. But as many mid-century modern home owners discover, the roof that imparts so much architectural verve can also present its own problems when form does not quite live up to function. Consequently, these nearly flat roofs seem to require more frequent roof maintenance and invariably the necessity for a new roof. Full picture gallery at end of post along with video of roof nine years after installation.
It was the rotting roof plywood, poor roof top drainage, and buckling composite roofing material from a previous re-roof that pushed us to figure out how best re-roof our home.
Mid-century Modern roofs are nearly flat
Our house is a Streng-type mid-century modern (MCM) home built in 1968. (I say Streng-type because Streng Brothers did not build the house. The original owners had the house design drafted using existing Streng homes in the Sacramento area as the model). There is 1,750 square of living space with a car port. When you add in the eaves we have approximately 2,600 square feet of roof. The roof pitch is 1:12 or pretty close to flat. In the MCM style, the roof had the downspouts built into the either side of the eave portion of the roof. A swale or gutter was created by the fascia board. The design was that this swale would capture the rain water and it would drain down one of several downspout holes in the roof.
Form can turn into failed function
I’m sure the built-in swale and downspouts work relatively well after the home was originally constructed with a tar and gravel roof. Sometime in the 1980’s or 90’s, before we bought the home in 2003, the original owner had a new roof installed. It was a three foot wide composite material, similar to composite shingles only in one long roll with the overlapping ends sealed with hot tar. There were some odd cut out in the eaves that I later figured out was the contractors way of dealing with the dry rot of the underlying plywood and fascia board.
Standing water on flat roofs creates dry rot
Initially tar and gravel, the original owner waited too long to re-roof and the roof contractor cut out sections the eaves that were compromised by dry rot. We have dry rot as well at the corners where the rain water would puddle. We could have an inch of water spread out over several square feet on the roof for days until it evaporated. The puddle was caused in part by clogged downspout openings but mainly a lack slope to direct the water to the hole in the roof. I knew this water would eventually soak through the composite roofing material and thoroughly wet the plywood and 2 x 6 fascia board. I attempted to waterproof the drainage swale at the edge of the roof with a layer of tar coating. The next year I added quickset cement to the roof gutter swale in an attempt to displace the standing water. In addition, I added a few more holes in the roof for the water to drain though in 2008.
Composite roofing buckled in summer heat
For the most part all these measures kept the roof relatively free from developing puddles after rainstorms. The black mildew that had plagued the underside of the roof plywood on the eave disappeared as it remained dry during the winter. Some of the holes would get clogged with pine needles, acorns, or leaves and I would have to sweep off the debris and unclog the holes so the rain water drained freely again. Over time I noticed that the composite roofing martial had separated from the base plywood and was causing bubbles. These little bubbles effectively stopped proper drainage. I can only assume that expansion and contraction from the heat of the sun caused this separation. Also during this time in 2013 I noticed the black mildew returning along with other fungi growing under the eaves.
My metal roof dream falls apart
I could no longer put off the inevitable – we had to get a new roof. After looking at all the options I had my heart set on a metal roof. Unfortunately, the metal roofers we attempted to get quotes from were not the most responsive or forthcoming with information. I was comfortable paying $10,000 more for a metal roof that would last a lifetime. The two issues that killed my dream were unresponsive contractors and the very real prospect of reduce or no cellular phone service. As we are not in a great cell area to begin with the thought of losing all mobile phone reception was not appealing.
Single ply PVC roof system
We finally turned our attention back to the two contractors who had quoted the single ply PVC roof system. They both used it exclusively for their flat roof customers and the majority of their business was either commercial or residential flat roofs in the Sacramento area. The quotes were essentially the same indicating both contractors were honestly bidding for the project. I personally liked both gentlemen. We finally chose one contractor over the other based on his willingness to correct the inherent drainage problem.
Finding the right contractor is the key
I had had enough of the built-in gutter swales that is traditional on MCM homes. I decided I wanted the rain water to sheet right off the roof into fascia gutters. Since the gutters are on the east and west side of the home and are not visible from the street, they’d have no impact on MCM nature of the house. One contractor really didn’t want to go with the fascia gutters but offered to enhance the directional flow of the rain water with crickets or standing seams in the roof material. He was also less inclined to repair the portions of the roof that had been cut away previously to remove dry rot sections. By contrast, the other roof contractor had no problems with correcting the cut out portions and adding full fascia gutters into the re-roof project. My gut feeling was that both the contractors would do an admirable job of re-roofing our house, but we went with the company that had no objection to installing the fascia gutters.
Quick tear off of old composite roof material
The tear off of the old composite roof took four hours. The new roof with the IB RoofSystems single ply 50 mil PVC material took four days to install, including the addition of new the fascia gutters and screen on top to keep out the leaves and acorns from our oak trees. The original polyiso-foam board, approximately one inch thick, was in good condition so we opted to keep it in place and just add another already order layer of polyiso-foam board. On top of this was a 3/8″ thick roll of a roofing felt material. Then the single ply PVC was rolled out over it.
Extra polyiso-foam might yield lower electrical bills
The extra foam board will give more insulation, but I never considered our home to be particularly hot in the summer or cold in the winter because of limited insulation as a result of the mid-century roof design. Our PG&E electrical hill has never exceeded more than $100. But we are judicious about running the air conditioner and the house is fairly small compared to some of the McMansions in the area.
Take lots of pictures to rebuild the roof puzzle
My own interest in the re-roof process compelled me to climb up on the roof each day after the workers had left to assess the progress and take pictures. While not everyone can hop up on a ladder and walk around their roof that is in a state of disrepair, my pictures did pay off. After the roof was installed I noticed that we might be missing an exhaust vent. But it was confusing because extra vents had been added to remove accumulated moisture from under the PVC material (membrane vents) and to vent the small interior space (attic vents) where the forced air duct work ran. The membrane vents are partially needed because our house was built without a ridge vent to draw off moisture from underneath the roofing material.
Where did I put that exhaust vent?
Each of the two bathrooms, the laundry room, and the kitchen has an electric exhaust fan that vents to the roof. In addition to the black vent pipe for the plumbing in each of those rooms, there should have been an exhaust vent. But there was nothing next to the kitchen plumbing vent pipe. We turned on the exhaust fan over the stove and found it was blowing air and accumulated dirt and dust into the space where the fan motor was located. Yep, the contractor completely covered up the hole in the roof that was the vent exit.
New exhaust vent was quickly added
This was a simple oversight as the form board was placed on the roof and a hole cut out for the plumbing vent pipe sticking out of the roof. The original roof vent rain shield was probably removed with the tear off. And since other portions of the roof had to have the plywood replaced because of dry rot, another hole in the plywood may have gone unnoticed. Either way, the contractor sent an employee out the next day and installed the exhaust vent. This job was made easier because I had snapped a picture of the vent pipe and exhaust hole so he knew exactly where to cut for the new vent. See pictures below.
Water should just cascade off the roof
It’s hard to get excited over spending $22,000 for essentially what amounts to maintenance on a house. However, I do have a sense of relief that I won’t be fighting water cascading off the end of my roof because of clogged downspouts. While the dry rot was not as extensive as we feared, I know the current roof will insure that the plywood and fascia boards stay relatively dry during rainstorms.
Updated gutters should extend life of roof and house
You can’t really see any of the new roof or gutters from either the street or the backyard. So even though the original design didn’t include fascia gutters, I don’t believe their addition detracts from the original mid-century modern design of the roof line. What good is a cool design if the result is a shortened life span or failure of a vital component to a house like the roof?
Winter Rains 2016
We’ve had a series of winter rain storms and the roof is performing as expected; the water runs off, it doesn’t create puddles on the roof, and there are no leaks. By far the most important feature we added are the rain gutters. Wow, what a difference a gutter makes. Instead of rain water sloshing over the edge of the because a drain hole was clogged by debris, the water sheets off into the fascia gutters, down the drain pipe and into the creek in the back yard. Before the new gutters the side yard were a mess with water splashing all over the place. The oak trees shed their acorns and would clog those little drain holes. Now with the wire mesh over the gutters and new downspouts I have not once had to don a rain coat and hat in the pouring rain to unclog those stupid holes. Winter is no longer a dreaded season with the new roof and rain gutter system.
Energy post script
It’s only been a couple of weeks since we had the new roof put on and we have already noticed a substantial decrease in how much the air conditioning is running. All I can attribute this to is the entirely white roof surface and extra-layer of iso-foam board. I work from home so am acutely aware of when the air conditioning kicks on. We have it set to come on 3:30 pm to cool the house down. But by 2:30 on a warm day it’s too hot to work in the front room office which gets most of the sun. While the front room is still warmer than the rest of the house, the area where the thermostat is located is not going over 80 degrees, which is the trip to activate the air conditioner. The air conditioner has automatically switched on a couple time in the evenings when we were making dinner.
I really didn’t think the new roof would have any impact on our inside temperature. But I was obviously wrong. So, that’s an unexpected bonus.
Nine Years After installation
I’ve received numerous comments and questions about the white roof and how it is holding up. I put together a little video to show what the PVC single ply roof looks like nine years after installation. We are still saving energy – and money – and the PVC roof is not as white, but in great shape.